Plastic extrusion services for specialized industrial applications
Plastic extrusion services for specialized industrial applications
Blog Article
A Comprehensive Guide to the Process and Advantages of Plastic Extrusion
In the huge world of manufacturing, plastic extrusion arises as a very reliable and vital procedure. Translating raw plastic right into continuous profiles, it caters to a variety of industries with its exceptional versatility.
Comprehending the Basics of Plastic Extrusion
While it might appear complex at very first look, the process of plastic extrusion is basically straightforward - plastic extrusion. It is a high-volume manufacturing technique in which raw plastic is melted and formed into a constant account. The procedure starts with the feeding of plastic material, in the form of granules, powders, or pellets, into a heated barrel. The plastic is then melted using a mix of warmth and shear, used by a turning screw. Once the molten plastic gets to completion of the barrel, it is compelled via a tiny opening referred to as a die, forming it right into a preferred type. The shaped plastic is after that cooled, strengthened, and cut into desired sizes, finishing the process.
The Technical Refine of Plastic Extrusion Explained

Kinds Of Plastic Suitable for Extrusion
The selection of the ideal kind of plastic is an essential element of the extrusion procedure. Numerous plastics provide one-of-a-kind properties, making them a lot more matched to particular applications. Polyethylene, for instance, is typically made use of because of its low cost and very easy formability. It uses excellent resistance to chemicals and dampness, making it perfect for products like tubes and containers. Similarly, polypropylene is an additional prominent selection due to its high melting point and resistance to exhaustion. For even more robust applications, polystyrene and PVC (polyvinyl chloride) are commonly picked for their stamina and durability. Although these are common options, the choice ultimately depends on the particular demands of the item being generated. So, comprehending these plastic types can substantially enhance the extrusion procedure.
Comparing Plastic Extrusion to Various Other Plastic Forming Approaches
Recognizing the kinds of plastic ideal for extrusion paves the way for a broader conversation on how plastic extrusion stacks up against various other plastic developing approaches. Plastic extrusion is exceptional when it comes to creating continuous accounts, such as seals, gaskets, and pipelines. It likewise permits for a constant cross-section along the length of the item.
Trick Advantages of Plastic Extrusion in Manufacturing
In the realm of manufacturing, plastic extrusion uses several substantial advantages. One noteworthy advantage is the cost-effectiveness of the procedure, which makes it a financially attractive production approach. Additionally, this strategy supplies exceptional item adaptability and improved production rate, therefore boosting total manufacturing performance.
Economical Production Technique
Plastic extrusion leaps see this here to the forefront as an affordable production approach in manufacturing. In addition, plastic extrusion requires much less energy than standard manufacturing methods, adding to reduced operational costs. In general, the monetary benefits make plastic extrusion an extremely appealing alternative in the production sector.
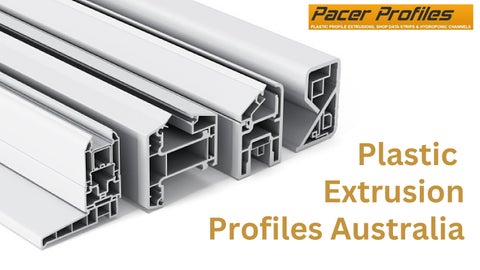
Superior Product Flexibility
Beyond the cost-effectiveness of plastic extrusion, an additional significant advantage in manufacturing depend on its exceptional item flexibility. This process enables the development of a wide range of products with differing dimensions, shapes, and styles, from easy plastic sheets to elaborate accounts. The versatility is credited to the extrusion pass away, which click here to find out more can be personalized to generate the preferred item layout. This makes plastic extrusion a suitable service for markets that require tailored plastic elements, such as automobile, building and construction, and product packaging. The capability to produce diverse products is not just beneficial in conference details market needs yet also in allowing manufacturers to discover brand-new product with minimal capital investment. Essentially, plastic extrusion's product flexibility fosters innovation while improving functional efficiency.
Improved Production Rate
A significant advantage of plastic extrusion hinges on its enhanced production speed. This manufacturing process enables for high-volume production in a reasonably brief time period. It is capable of producing long, continual plastic profiles, which considerably decreases the production time. This high-speed manufacturing is particularly advantageous in industries where big quantities of plastic components are needed within limited due dates. Couple of other production procedures can match the site speed of plastic extrusion. In addition, the capability to preserve constant high-speed manufacturing without compromising product high quality sets plastic extrusion in addition to other approaches. The improved production speed, for that reason, not only makes it possible for producers to meet high-demand orders however also adds to raised efficiency and cost-effectiveness. This beneficial function of plastic extrusion has actually made it a recommended option in many markets.
Real-world Applications and Impacts of Plastic Extrusion
In the realm of manufacturing, the method of plastic extrusion holds extensive value. The economic advantage of plastic extrusion, mostly its cost-effective and high-volume result, has reinvented production. The industry is persistently aiming for technologies in recyclable and naturally degradable products, indicating a future where the benefits of plastic extrusion can be kept without endangering ecological sustainability.
Conclusion
To conclude, plastic extrusion is a extremely effective and reliable technique of changing raw products right into varied items. It supplies countless benefits over various other plastic creating methods, including cost-effectiveness, high output, minimal waste, and design flexibility. Its influence is profoundly felt in various sectors such as construction, automotive, and consumer items, making it a critical process in today's production landscape.
Delving much deeper right into the technological procedure of plastic extrusion, it begins with the selection of the suitable plastic material. Once cooled, the plastic is cut into the required sizes or injury onto reels if the item is a plastic film or sheet - plastic extrusion. Contrasting Plastic Extrusion to Various Other Plastic Forming Approaches
Recognizing the types of plastic ideal for extrusion paves the way for a more comprehensive discussion on just how plastic extrusion stacks up versus other plastic forming techniques. Few various other manufacturing procedures can match the speed of plastic extrusion.
Report this page